OEIS/FASS curves: Difference between revisions
imported>Gfis polyamide and glass cube |
imported>Gfis No edit summary |
||
Line 54: | Line 54: | ||
* as a '''[http://teherba.org/threejs/meander-box.html solid 3D model]''' | * as a '''[http://teherba.org/threejs/meander-box.html solid 3D model]''' | ||
===3D Manufacturing=== | ===3D Manufacturing=== | ||
[[File:trinckle-box.jpg|250px|right|4x4 cm cube (polyamide sintering)]] | |||
All my attempts to physically build such objects were unsatisfying so far. The balsa lumber and the Fischertechnik approaches worked somehow, but both needed distance bars (thin needles for the balse, red blocks for Fischertechnik) to keep the geometry in shape. Cutting and glueing of the 62 balsa parts was very tedious. | |||
In discussions with several people I learned that such FASS curves cannot be produced by conventional processes like milling or die casting. Therefore I tried the current hype of 3D printing. | |||
With Three.js it is also very easy tp store an [https://en.wikipedia.org/wiki/STL_(file_format) STL] file derived from the virtual scene. STL is the main format for stereolithography CAD software, 3D printers and other manufacturing devices. STL stores a ''mesh'', that is a set of triangles representing the geometry of the object. | With Three.js it is also very easy tp store an [https://en.wikipedia.org/wiki/STL_(file_format) STL] file derived from the virtual scene. STL is the main format for stereolithography CAD software, 3D printers and other manufacturing devices. STL stores a ''mesh'', that is a set of triangles representing the geometry of the object. | ||
* Download the '''[http://teherba.org/threejs/meander-box.stl meander STL file]''' and view it with the free service of [https://www.viewstl.com/ viewstl.com], and/or | * Download the '''[http://teherba.org/threejs/meander-box.stl meander STL file]''' and view it with the free service of [https://www.viewstl.com/ viewstl.com], and/or |
Revision as of 19:17, 3 October 2017
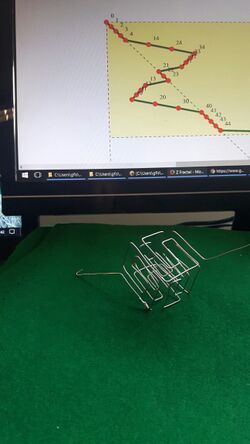
Beyond OEIS sequence A220952
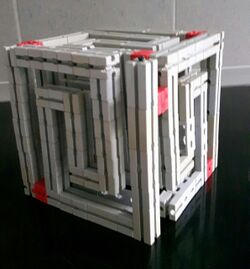
Sequence A220952 is best discussed with numbers to base 5. The first 125 values then are:
0, 1,2,3,4, 14,24,34,33,32,31,21,22,23,13,12,11,10,20,30,40,41,42,43,44, 144,244,344,343,342,341,241,242,243,143,142,141,140,240,340, 330,320,310,210,220,230,130,120,110,111,112,113,123,122,121, 131,132,133,233,232,231,221,222,223,213,212,211,311,312,313, 323,322,321,331,332,333,334,324,314,214,224,234,134,124,114, 104,204,304,303,302,301,201,202,203,103,102,101,100,200,300, 400,401,402,403,404,414,424,434,433,432,431,421,422,423,413, 412,411,410,420,430,440,441,442,443,444
In each generation the number of digits is increased by one. The first 25 values form the adjacency condition matrix as defined by Knuth:
04==14==24==34 44 || || || 03 13==23 33 43 || || || || || 02 12 22 32 42 || || || || || 01 11 21==31 41 || || || 00 10==20==30==40
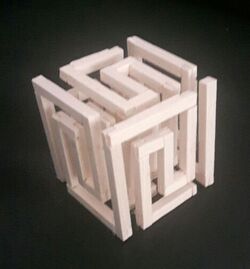
Here, the last digit is the y coordinate, and the digit before is the x coordinate. In generation 3, the left-most digit can be interpreted as the z coordinate. Since this is Knuth's original adjacency matrix, and since it shows a letter "n", I named it "Kn".
The curve is space-filling in every dimension
For the cube I wrote a Javascript program with the beautiful framework three.js.
Variants
There is another, trivial matrix:
04==14 24==34 44 || || || || || 03 13 23 33 43 || || || || || 02 12 22 32 42 || || || || || 01 11 21 31 41 || || || || || 00 10==20 30==40
A third adjacency matrix shows the structure of the letter "F" and "s", therefore I named it "Fs":
04==14==24==34 44 || || || 03 13==23==33 43 || || || 02 12==22==32 42 || || || 01 11==21==31 41 || || || 00 10==20==30==40
The corresponding cube can be viewed:
- as a colored line with coordinates
- as a solid 3D model
3D Manufacturing
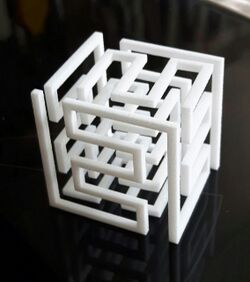
All my attempts to physically build such objects were unsatisfying so far. The balsa lumber and the Fischertechnik approaches worked somehow, but both needed distance bars (thin needles for the balse, red blocks for Fischertechnik) to keep the geometry in shape. Cutting and glueing of the 62 balsa parts was very tedious.
In discussions with several people I learned that such FASS curves cannot be produced by conventional processes like milling or die casting. Therefore I tried the current hype of 3D printing.
With Three.js it is also very easy tp store an STL file derived from the virtual scene. STL is the main format for stereolithography CAD software, 3D printers and other manufacturing devices. STL stores a mesh, that is a set of triangles representing the geometry of the object.
- Download the meander STL file and view it with the free service of viewstl.com, and/or
- send the STL file to the production service company of your choice.
During a holiday in Greece I sent such a file to trinckle.com in Germany, and within 10 days and 20 € I received the nice 4x4 cm cube on the right. It was made by sintering plastic (polyamide) with a laser. The problem is that the structure cannot be built on a supporting surface, and that there is some warping caused by the heat of the laser and the weight of the material. The object is very fragile.
In the next step I will order a 5x5 cm internally engraved glass cube from easycrystal.de for about 40 €. Such a cube is very stable, and the engraved point cloud for the FASS curve is geometrically exact.